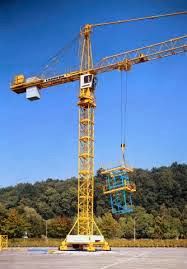.jpg)
Handle Construction Plant and Equipment Smartly
Check construction plant and equipment before go to start your work. No compromise for the issue of safety induction: Also keep in mind the most common thing to do
is to store this item in a safe location until it is needed. I would also
submit some type of documentation to the sub making sure they know if the item
is damaged or misused.
Hoists
Dumper Tracks
Cranes
Excavators
Compressors
Fork Lift Trucks
Concrete Mixers
Compactors
When using HOISTS, check:
ØThe equipment been installed by a competent person?
ØAre the operators trained and competent?
ØIs the rated capacity clearly marked?
ØDoes the hoists have current report of through
examination and a record of inspection?
ØIs there a suitable bas enclosure to prevent people from
being struck by any moving part of the hoists?
ØAre the landing gates kept shut except when the platform
is at the landing?
When using DUMPER trucks, check:
ØLoad carried are
within the capacity of the dumper truck?
ØNo passengers to ride
on the dumper
ØSpeed limits are not
exceeded when carrying loads?
ØNo traveling over
steep embankments and rough terrains?
ØNo sharp turning to
avoid overturning of dumper?
ØTyres are at the correct
inflated pressure?
ØOperators are trained
and competent?
Sponsored:
Sponsored:
If CRANES are on site, check:
ØNo riding on the
crane hooks?
ØThe carrying capacity
is being adhered to?
ØExclusion zones
created for lifting over public?
ØCrane operator being
directed by trained Dogman?
ØSecuring of loads
being done by trained Riggers?
ØEnsure all lifting
gear is current?
ØAccess is restricted
to authorized personnel?
ØWarning signs on
overhead work in progress displayed about the site?
When using EXCAVATORS, check:
ØOperators to be
trained and competent?
ØNo passengers to ride
on the excavators?
ØSpeed limits are not
exceeded when carrying loads?
ØNo travelling near to
edge of excavations?
ØAll warning signals
are operating?
ØA banksman to be used during
operations?
ØLocations of any
buried cables and pipes?
When working with COMPRESSORS, check:
ØAll hoses are uncoiled and protected from damage?
ØThe components are correctly installed and attached
securely to each other?
ØCompressor is located as far away as possible from the
worker?
ØObservation of safe work practices and exclusion zones?
ØCorrect personal protective equipments is being worn, eg. Had hat, safety
boots, gloves and hearing protectors?
ØThe compressor pressure safety valve is functional?
When using FORK LIFT trucks, check:
ØOperators to be trained and competent?
ØNo passengers to ride on fork lift trucks?
ØSpeed limits are not exceeded when carrying loads?
ØNo traveling at speed around corners?
ØAll warning signals are operating?
ØGas powered fork lift trucks not to be used in enclosed
spaces?
ØWarning signs of fork lift truck in operation to be
posted?
ØReversing siren and lights to be operational?
ØThe correct load charts are displayed on the forklift?
If working with CONCRETE MIXERS, check:
ØAll moving parts are secured when in transport?
ØThe truck is “locked off” before cleaning the drums?
ØTrucks not parked too close to excavation edge?
ØObservation of safe work practices and exclusion zones?
ØCorrect personal protective equipments is being worn, eg. Had hat, safety
boots, gloves and hearing protectors?
ØObservation of safe disposal of excess concrete?
ØReversing signals ie.
Light and siren are operational?